Supply Chain Management Automated Shipment & Tracking System
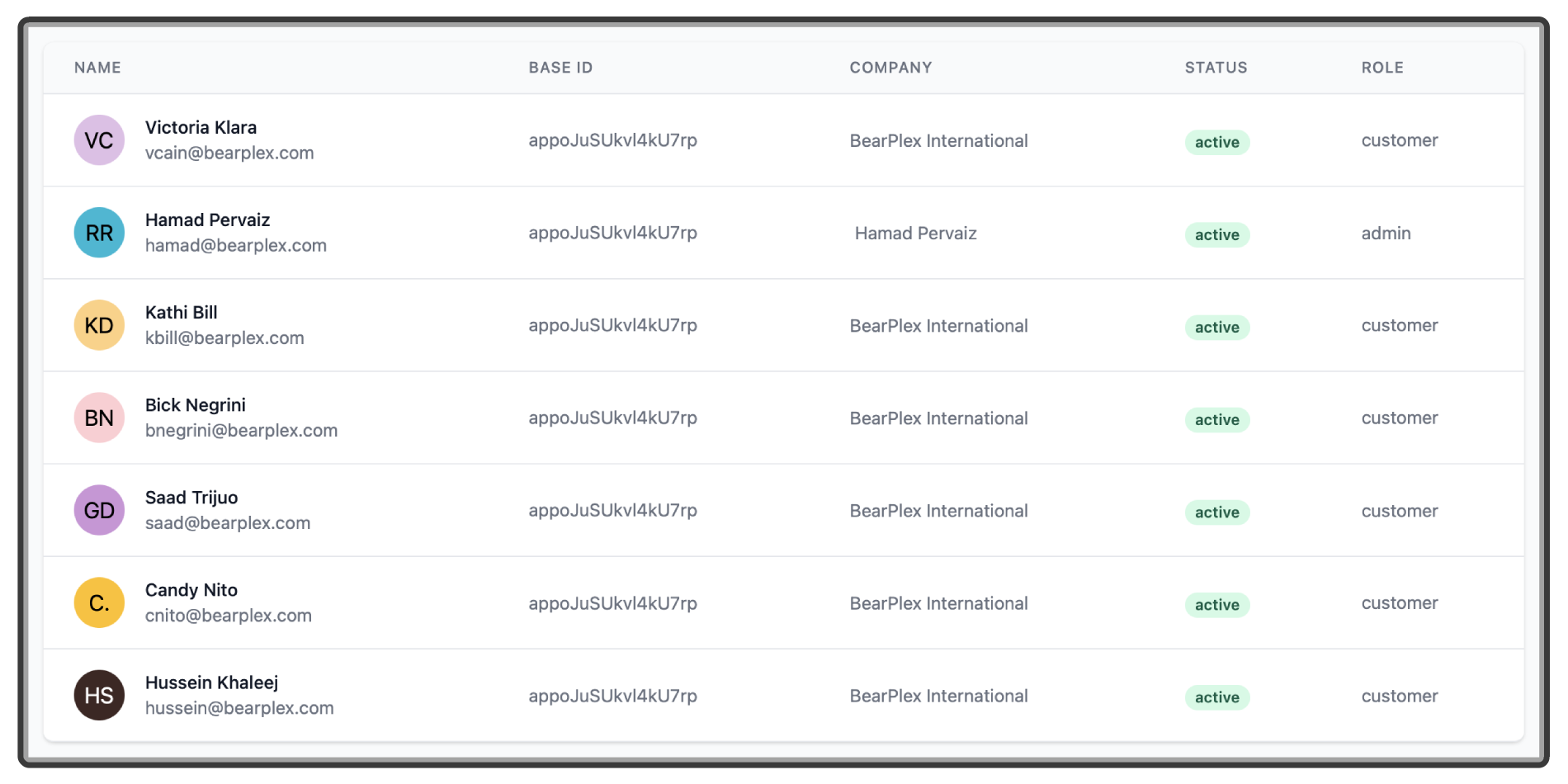
Client Background
A leading supplier of Personal Protective Equipment (PPE) faced unprecedented logistical challenges during the COVID-19 pandemic. The company managed hundreds of containers shipping from factories in China to clients across the US and Canada via air and sea, often coordinating multiple shipments daily. Their rapid growth exposed inefficiencies in manual tracking, reporting, and client communication, threatening their ability to scale.
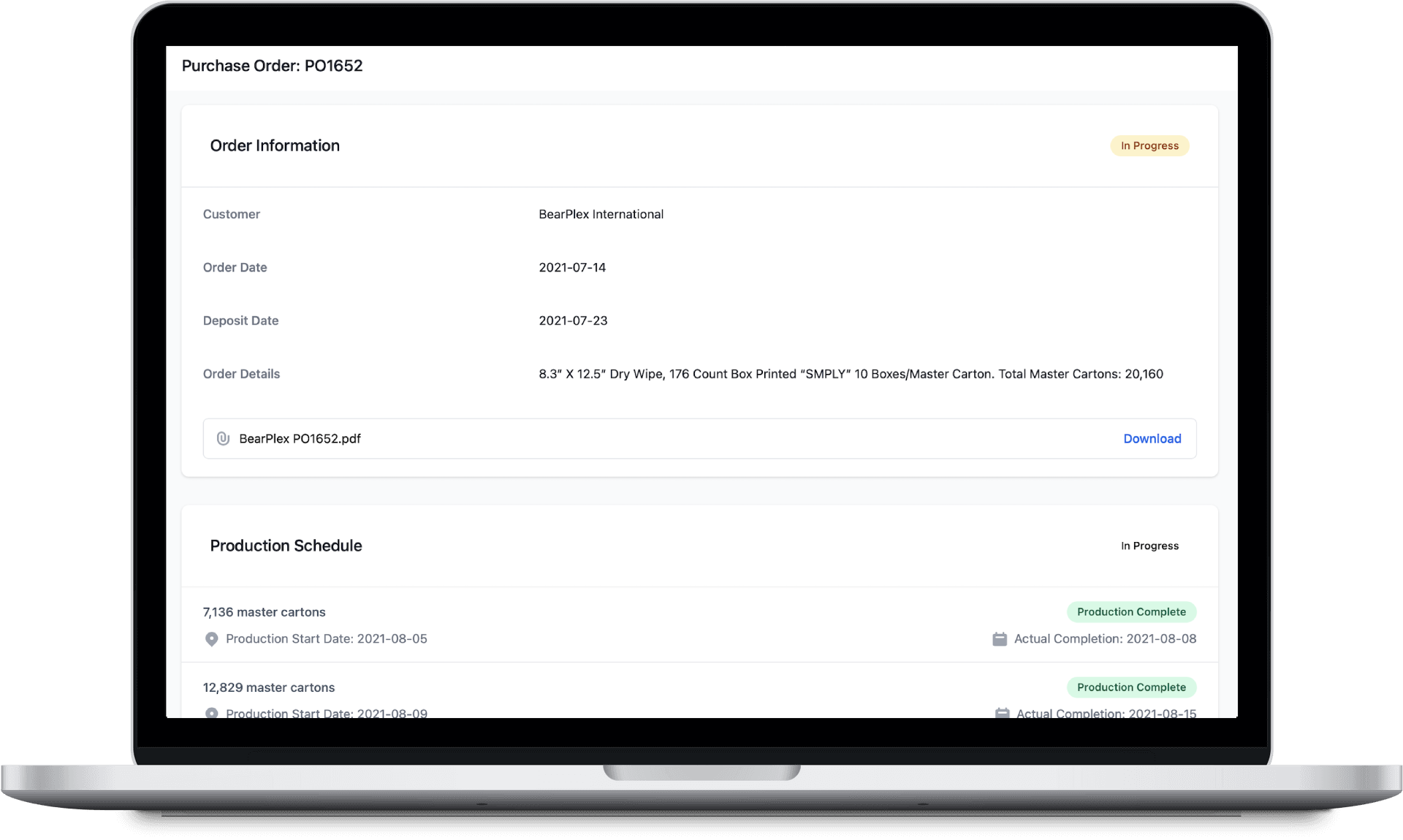
The Challenge
Scale & Complexity: Managing hundreds of containers across air and port shipments, with real-time updates required for clients.
Manual Processes: Daily reporting was time-consuming, error-prone, and unsustainable for their growing operations.
Lack of Transparency: Clients had no visibility into production progress, shipment status, or documentation (e.g., photos of loaded containers).
Competitive Edge: The company needed a unique selling proposition (USP) to secure high-value contracts, including government tenders.
The Solution
We designed and deployed a fully automated shipment management and tracking system tailored to streamline end-to-end logistics. The platform integrated AI-driven automation, real-time data aggregation, and a client-facing portal to solve critical pain points.
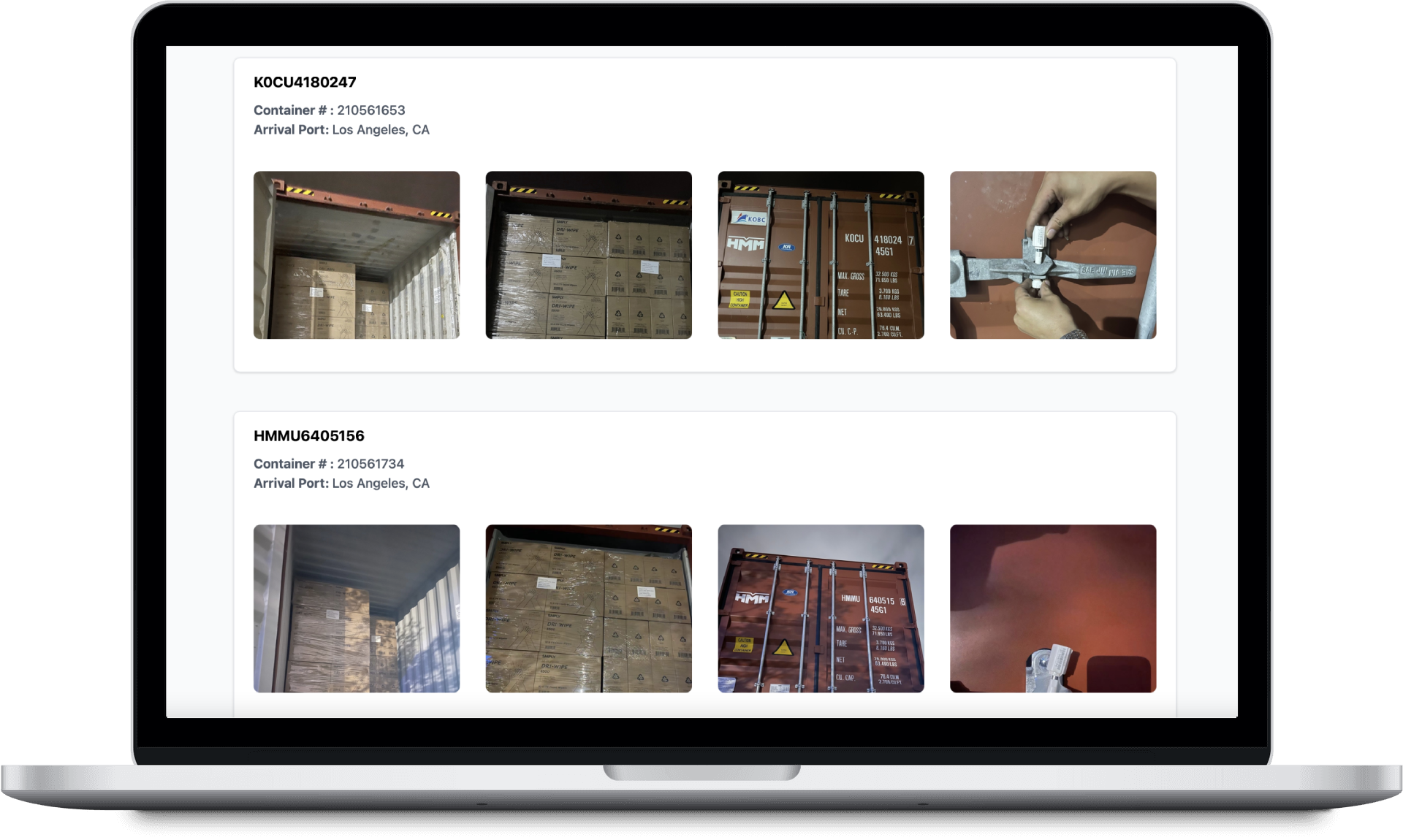
Key Features
Real-Time Production Monitoring
Factories in China updated production statuses directly into the system, eliminating communication delays.
Multi-Modal Shipment Tracking
Automated updates for air and sea shipments, including carrier data integration (e.g., port ETAs, flight schedules).
Automated Documentation & Imaging
Photos of loaded containers, packing lists, and customs documents were uploaded automatically to each order.
Centralized Client Portal
Clients accessed a dashboard to view order statuses, track shipments globally, and download compliance documentation.
Scalable Architecture
Built to handle thousands of concurrent users and container updates without performance lag.
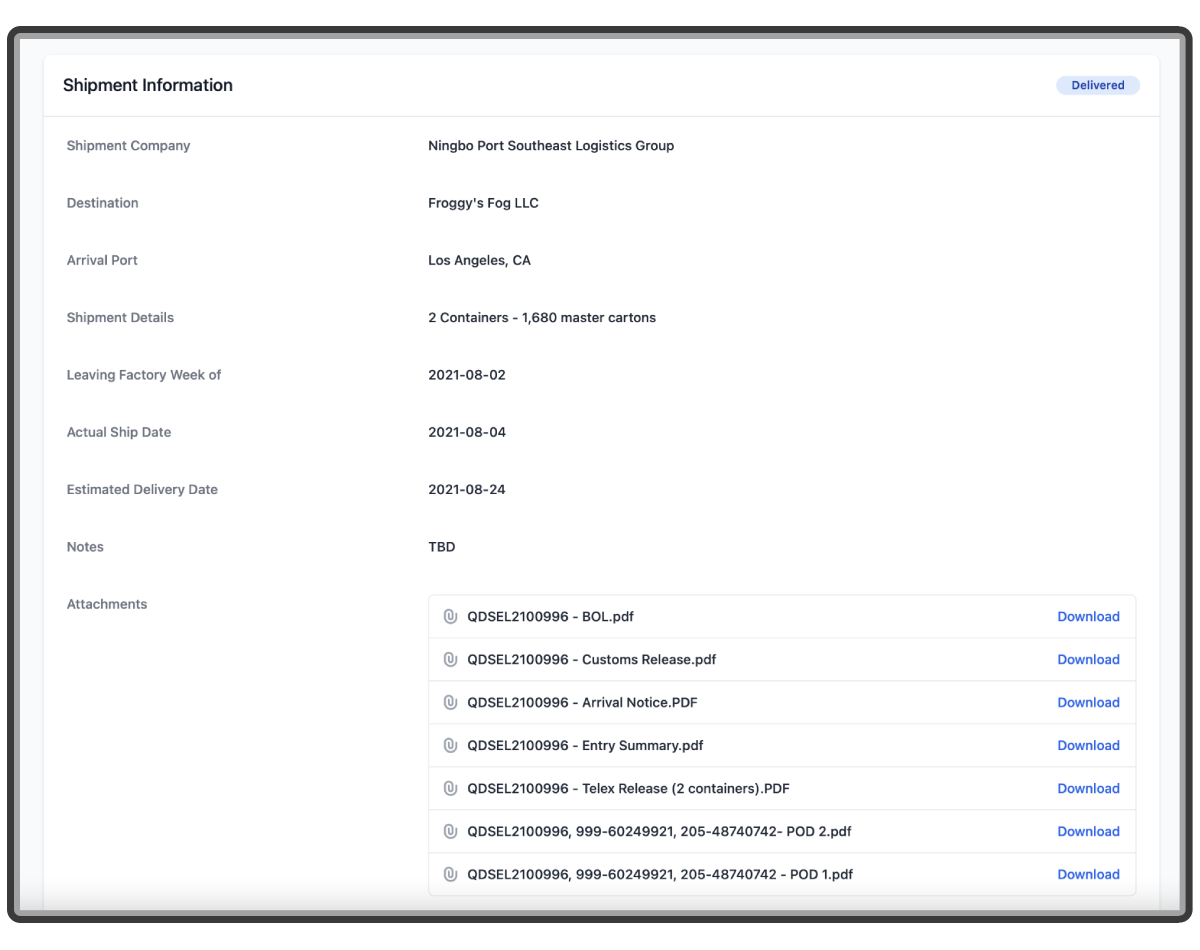
The Results
100% Elimination of Manual Reporting
Daily reports were generated and shared automatically, saving 40+ hours/week of manual work.
Enhanced Client Trust & Satisfaction
Real-time transparency reduced client inquiries by 70% and improved retention.
USP for Multi-Million Dollar Contracts
The system became a cornerstone of the company’s sales strategy, helping them secure a landmark government contract.
Operational Scalability
The platform enabled seamless management of 500+ containers/month, positioning the company as a leader in PPE logistics.
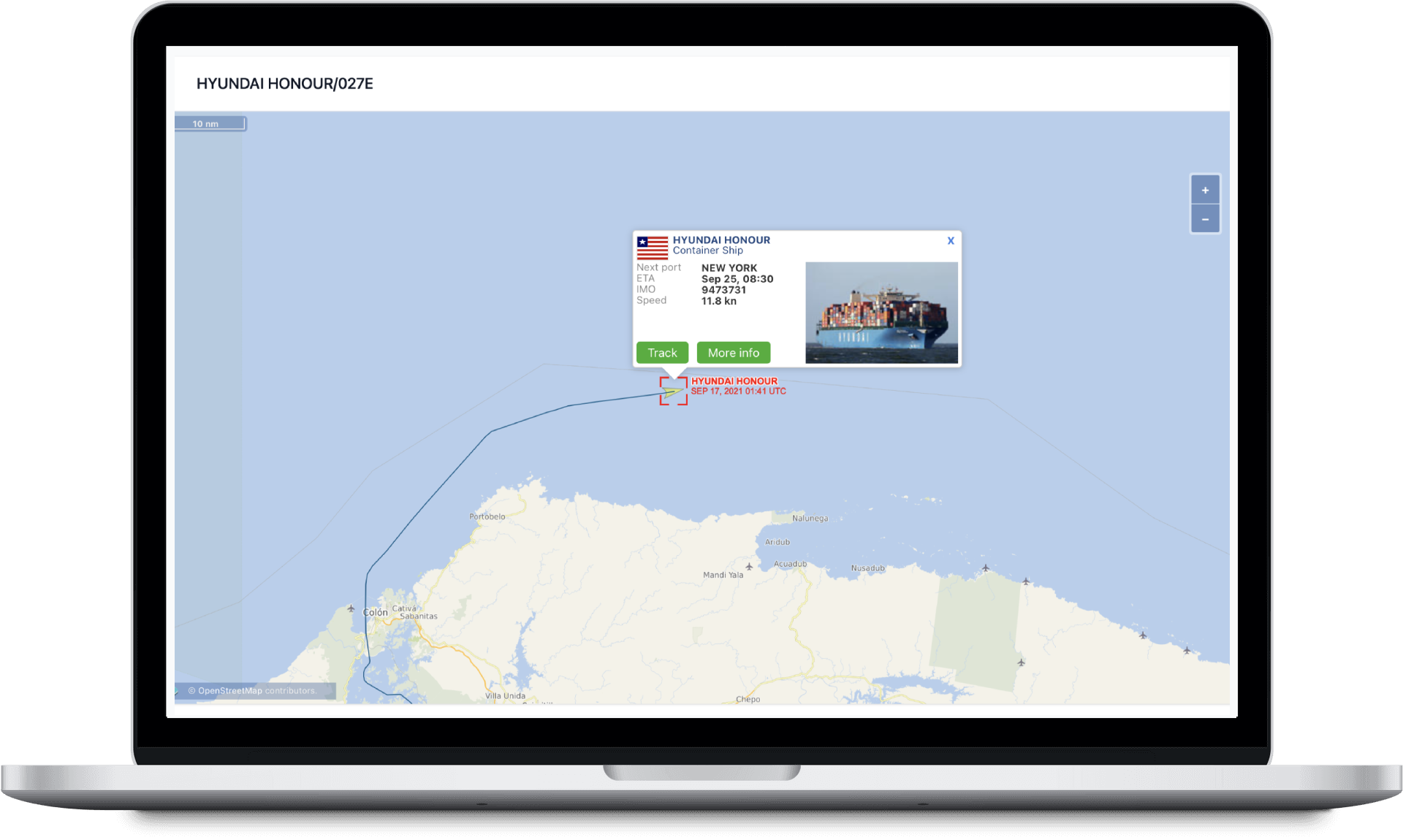
This project exemplifies how our AI integration and custom software modernization can transform complex operations into competitive advantages. By automating workflows and centralizing data, businesses can scale efficiently, reduce costs, and deliver unmatched value to clients.